Caterpillar (CAT) 307B 308B Sprocket 51-9336 23T (Fit Caterpillar (CAT) 307 307B Mini Excavator)
Basic Info.
- Item Fit: Caterpillar (CAT) 307 307B
- Item Condition: New
- Item Weight: 49 lbs
- Item Maker: FLundercarriage
- Place of Origin: Quanzhou
Delivery Info.
- Inventory Class: Standing
- Packaging: Carton/Pallet
- ETD: 24-72 Hours
- ETA: 5-30 Days
- Sprocket Compatibility: Specially designed for Caterpillar 308B, 307B, and 307 models within specific serial ranges.
- Features: This sprocket comes with twenty-three drive teeth and is secured with twelve bolts.
- Improved Longevity: For the best performance and to avoid premature wear, it's recommended to change both your undercarriage parts and rubber tracks concurrently.
- Caterpillar Part Number: Recognized by Caterpillar Dealer Part Number 51-9336.
- Serial Prefix Compatibility: This sprocket fits machines with serial prefixes S/N 2FL, 2PM, 2WM, 9ZL, AFB, 3YS. If your machine requires a sprocket with 21 teeth, please refer to the Cat 307 series sprocket for proper fit.
- Caterpillar 307
- Caterpillar 307B
- Caterpillar 308B
- Durability: Our sprockets are hardened through an efficient one-step electrical induction process. This method not only increases the hardness depth of the teeth but also significantly reduces the risk of breakage.
- OEM Comparable: Engineered to match the durability and performance metrics within millimeters of the original equipment manufacturer (OEM) sprocket.
- Simple Installation: For optimum results, we advise manually installing this sprocket following the torque specifications recommended by your manufacturer.
В наличии: 153
Share This Product

Flundercarriage Show
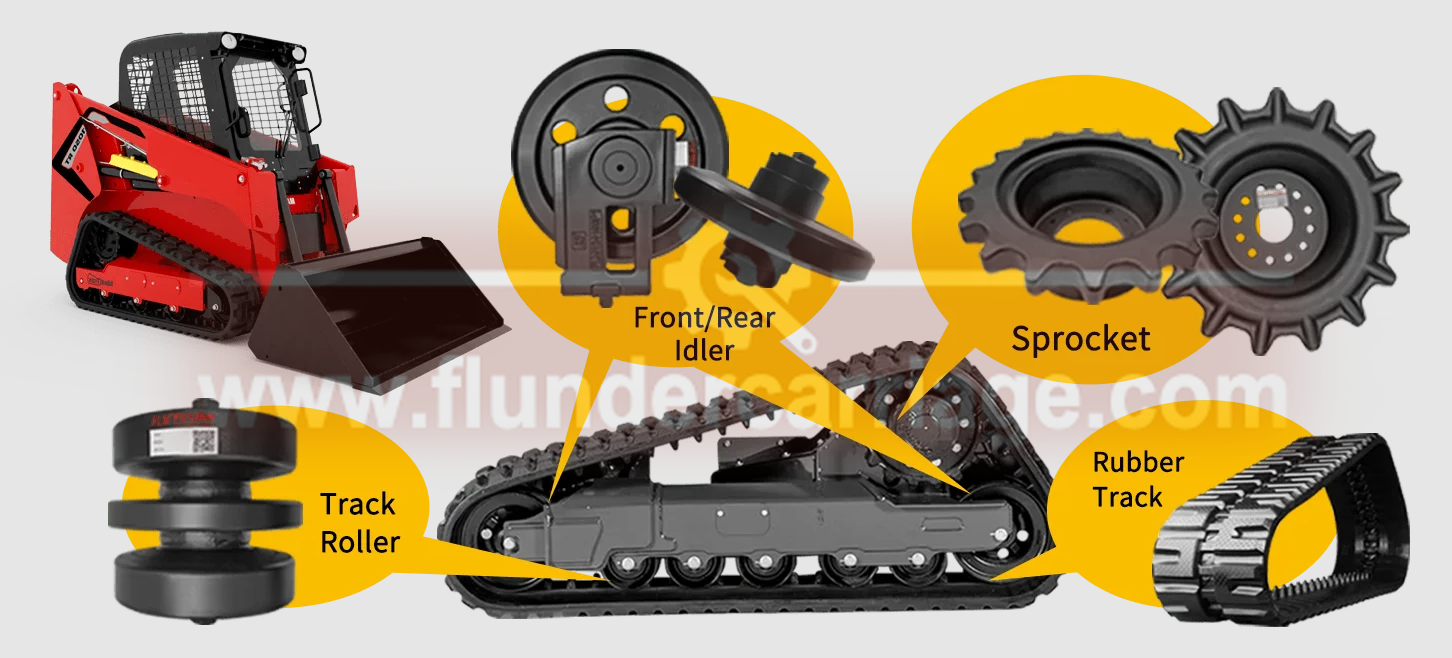
Why Choose FL Undercarriage
-
20+ Years Experience
-
100+ Dealers Globally
-
300000+ stock Keeping units
-
50000000+ USD Annual sales
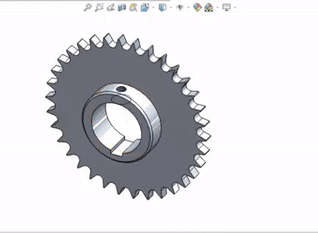
Product Range
Our sprockets are built to withstand extreme conditions, ensuring smooth and efficient power transmission in your machinery. Crafted from high-quality materials, they offer exceptional wear resistance and durability, making them ideal for heavy-duty applications. Trust our sprockets to enhance the performance and longevity of your equipment, keeping operations running smoothly.
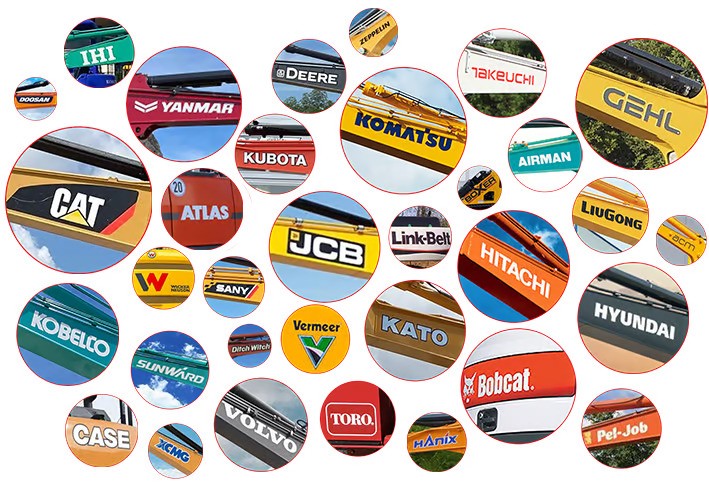
Machinery brands our parts are suitable for Bobcat, Caterpillar, Case, Doosan, GEHL, Hitachi, Hyundai, IHI, Kubota, Kobelco, Komatsu, Pel-Job, Takeuchi, Volvo etc.
How are your sprockets produced
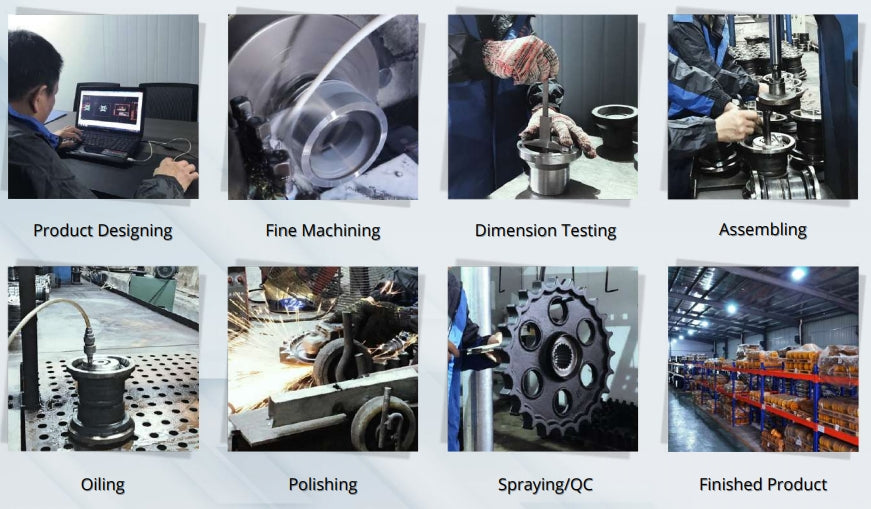
Trade Show Events
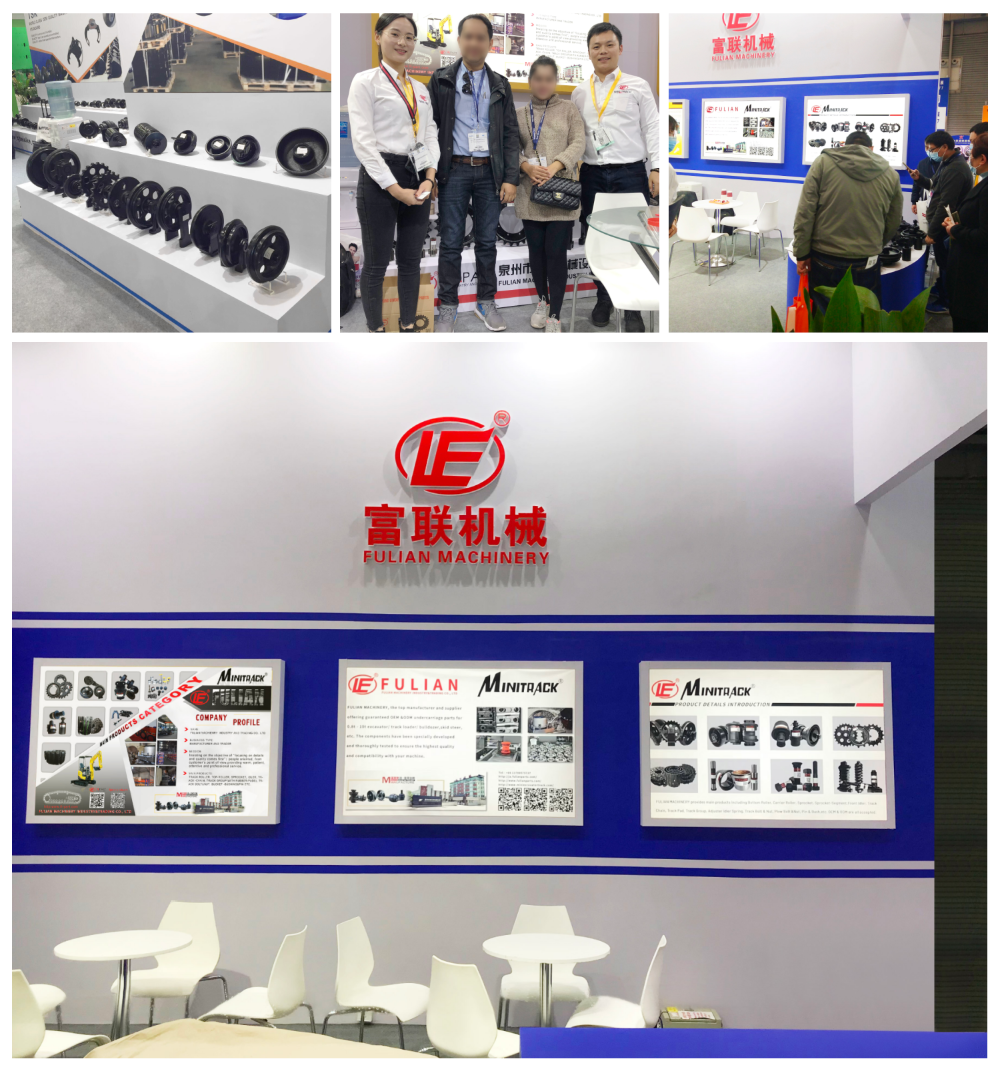
Customer reviews
FAQ
How often do excavator sprockets need to be changed?
A sharp gear indicates that the gear is worn. Check whether there are grooves around and under the gear that are similar to the chain shape. This "shadow" wear indicates that the gear has been seriously worn and should be replaced.
What are the contributing factors that lead to the deterioration of sprockets on an excavator?
Several factors lead to wear and tear of excavator sprockets, including:Heavy usage, Abrasive environments, Improper track tension, Inadequate maintenance, Rough operation, Quality of the sprockets, Misalignment of components, Age and metal fatigue
What maintenance routine can I follow to ensure my excavator sprockets last longer?
To extend the life of your excavator sprockets, implement a maintenance routine that includes:Regular cleaning of debris and dirt,Frequent inspections for wear,Ensuring correct track tension,Prompt replacement of worn parts,Lubrication to reduce friction,Using high-quality replacement sprockets,Operator training to prevent harsh handling.