Case - New Holland Track Loader Sprockets (Fit New Holland LT185B LT190B Loader)
Basic Info.
- Item Fit: New Holland LT185B LT190B
- Item Condition: New
- Item Weight: 60 lbs
- Item Maker: FLundercarriage
- Place of Origin: Quanzhou
Delivery Info.
- Inventory Class: Standing
- Packaging: Carton/Pallet
- ETD: 24-72 Hours
- ETA: 5-30 Days
- Teeth Count: 17
- Bolt Count: 8
- Inside Diameter: 9 inches
- Outside Diameter: 18 1/2 inches
- Width at Widest Point: 1 7/8 inches
- Reuse Factory Bolts: Designed for easy installation, allowing you to use your existing factory bolts.
- Recommended Replacement: For optimal performance and elongated lifespan, it's advised to replace sprockets and tracks simultaneously.
- Torque Requirements: Always hand-tighten to the manufacturer's specified torque to prevent damage.
- Case Dealer Part Number: 47378993
- New Holland Dealer Part Numbers: 87447232, 87371666, CA963
- New Holland: C175, C185, C190, C195, LT185B, LT190B, C227, C232, C234, C237, C238, C245, C332, C337
- Case: CT420, CT440, CT445, CT450, TV370, TV380, TV450, TR270, TR310, TR320, TR340
- Sprockets
- Rear Idlers
- Front Idlers
- Bottom Rollers
200 in stock
Share This Product
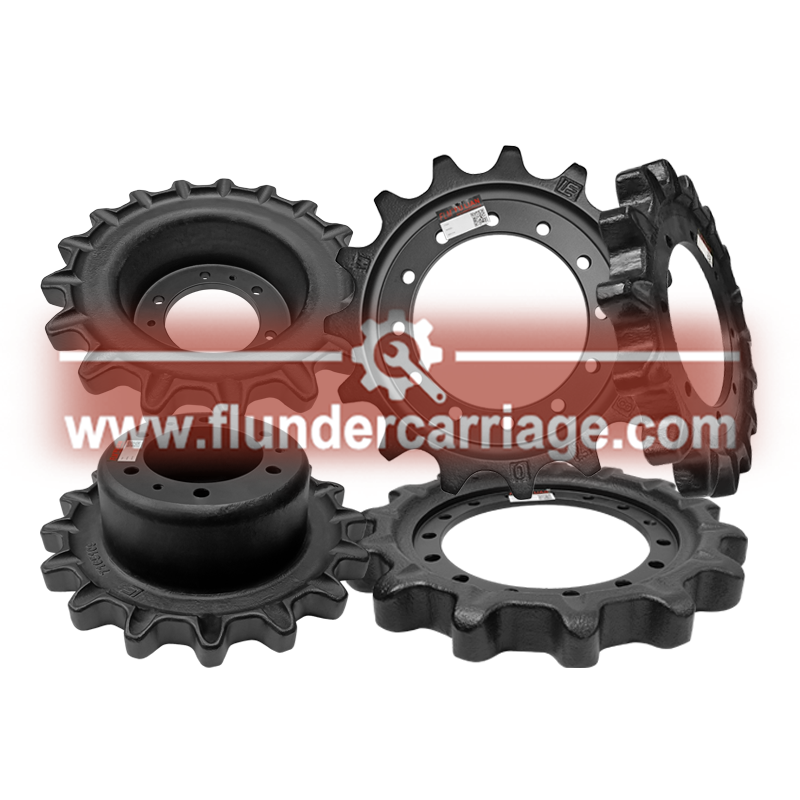
Flundercarriage Show
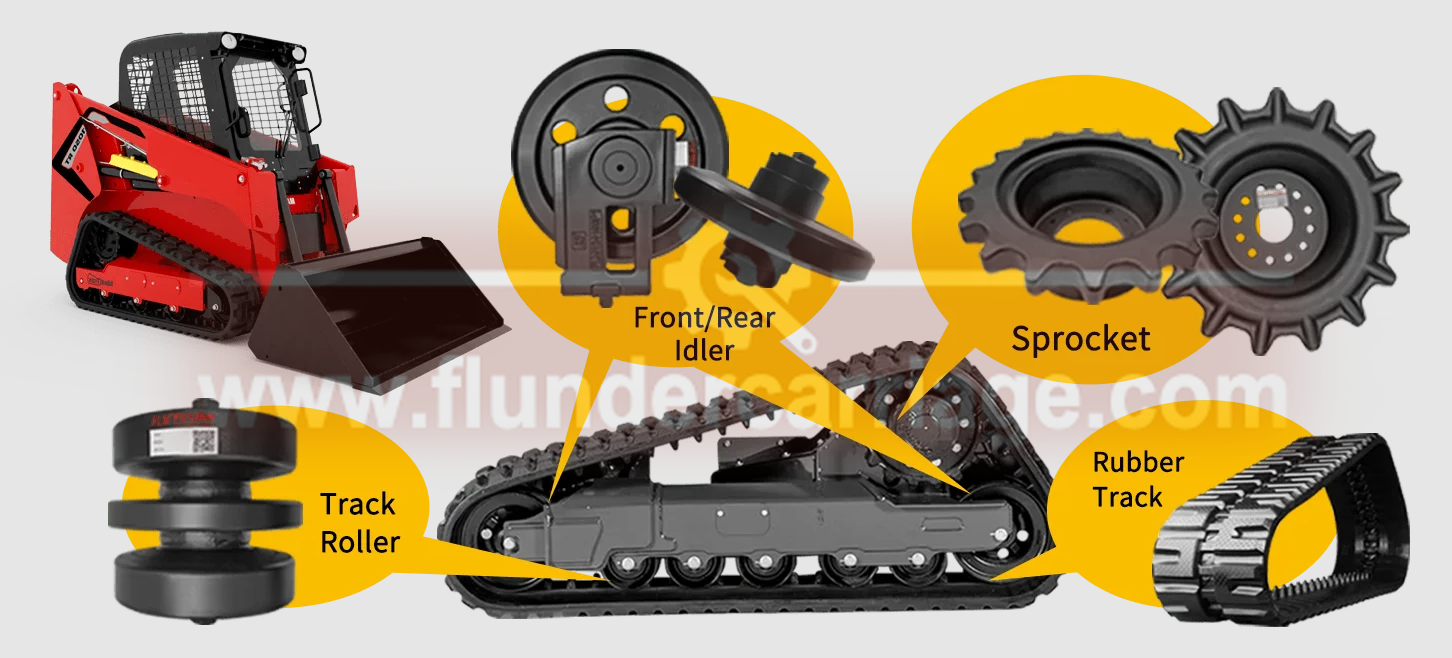
Why Choose FL Undercarriage
-
20+ Years Experience
-
100+ Dealers Globally
-
300000+ stock Keeping units
-
50000000+ USD Annual sales
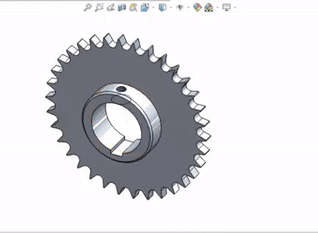
Product Range
Our sprockets are built to withstand extreme conditions, ensuring smooth and efficient power transmission in your machinery. Crafted from high-quality materials, they offer exceptional wear resistance and durability, making them ideal for heavy-duty applications. Trust our sprockets to enhance the performance and longevity of your equipment, keeping operations running smoothly.
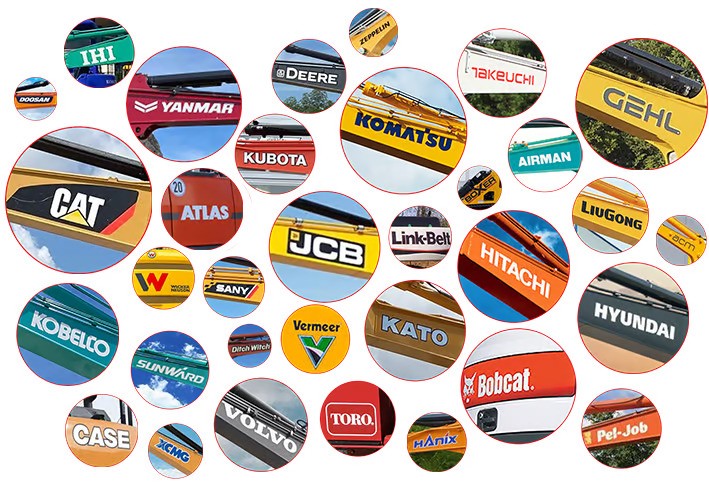
Machinery brands our parts are suitable for Bobcat, Caterpillar, Case, Doosan, GEHL, Hitachi, Hyundai, IHI, Kubota, Kobelco, Komatsu, Pel-Job, Takeuchi, Volvo etc.
How are your sprockets produced
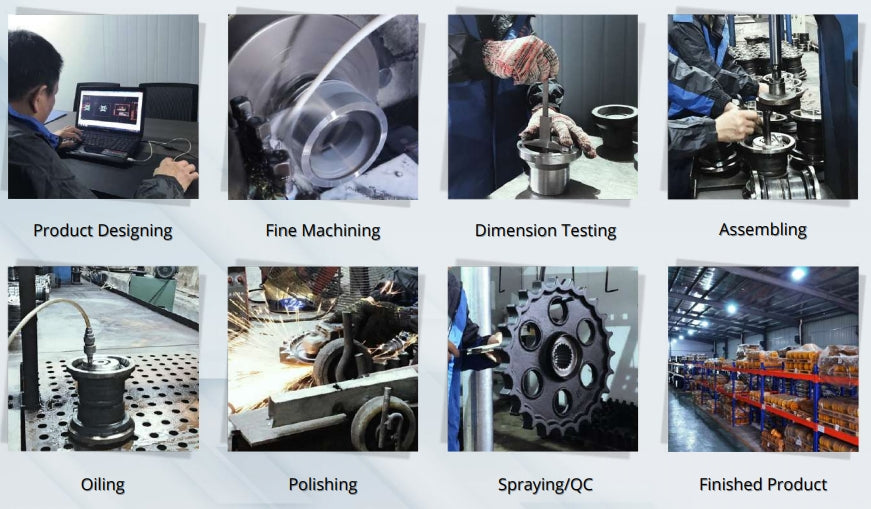
Trade Show Events
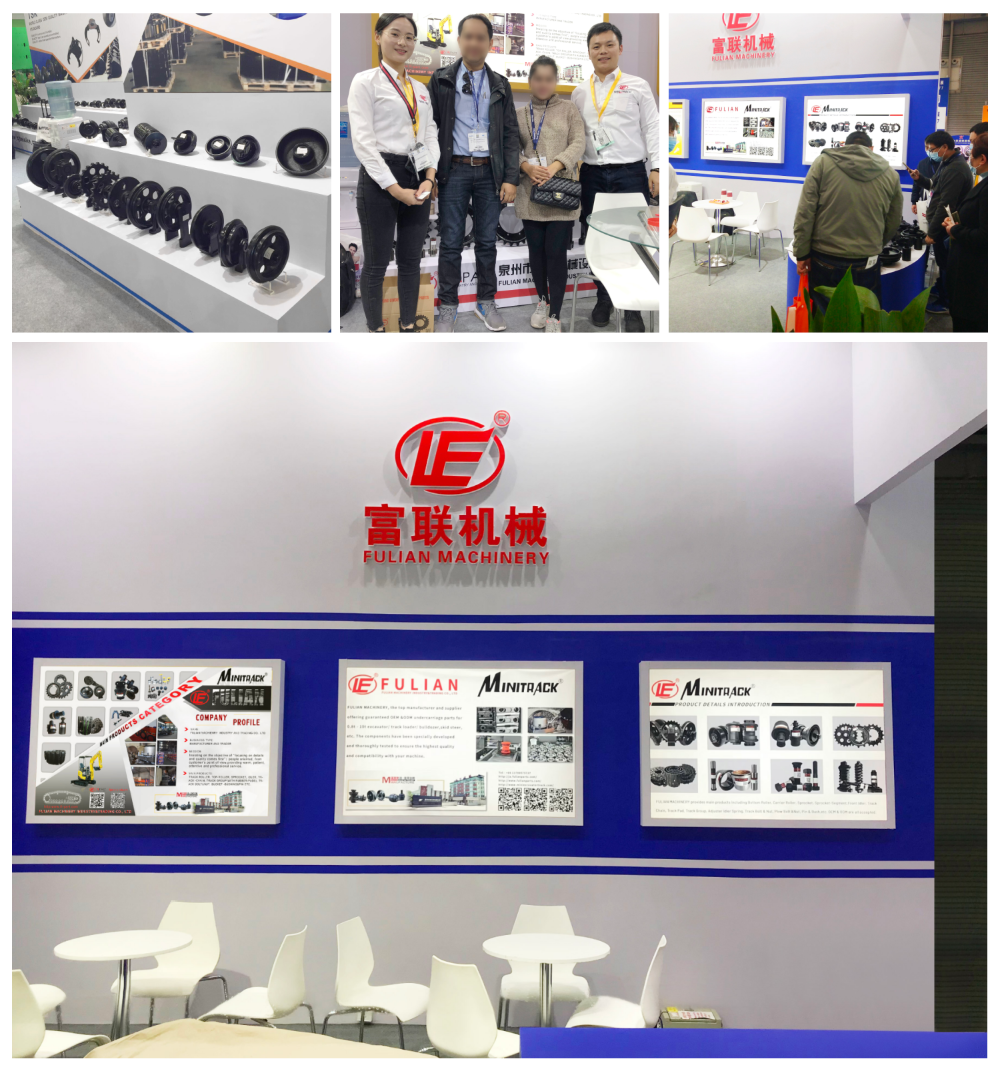
Customer reviews
FAQ
How often do excavator sprockets need to be changed?
A sharp gear indicates that the gear is worn. Check whether there are grooves around and under the gear that are similar to the chain shape. This "shadow" wear indicates that the gear has been seriously worn and should be replaced.
What are the contributing factors that lead to the deterioration of sprockets on an excavator?
Several factors lead to wear and tear of excavator sprockets, including:Heavy usage, Abrasive environments, Improper track tension, Inadequate maintenance, Rough operation, Quality of the sprockets, Misalignment of components, Age and metal fatigue
What maintenance routine can I follow to ensure my excavator sprockets last longer?
To extend the life of your excavator sprockets, implement a maintenance routine that includes:Regular cleaning of debris and dirt,Frequent inspections for wear,Ensuring correct track tension,Prompt replacement of worn parts,Lubrication to reduce friction,Using high-quality replacement sprockets,Operator training to prevent harsh handling.