Caterpillar (CAT) 259B3 259D Sprockets 304-1870 (Fit Caterpillar (CAT) 239D 249D Loader)
Basic Info.
- Item Fit: Caterpillar (CAT) 239D 249D Loader
- Item Condition: New
- Item Weight: 43 lbs
- Item Maker: FLundercarriage
- Place of Origin: Quanzhou
Delivery Info.
- Inventory Class: Standing
- Packaging: Carton/Pallet
- ETD: 24-72 Hours
- ETA: 5-30 Days
- Caterpillar 239 Series: 239D / DR, 239 DLRC
- Caterpillar 249 Series: 249D / D3, 249 DLRC
- Caterpillar 259 Series: 259B3, 259D, 259D3, 259 DLRC
- Teeth Count: 15 teeth for optimum engagement
- Bolt Holes: 12 bolt holes for secure installation
- Inside Diameter: 8 5/8 inches to match the hub perfectly
- Outside Diameter: 16 3/4 inches for balanced rotation
- OEM Comparable Quality: Drive teeth are induction hardened just millimetres off OEM specifications, ensuring long-lasting performance.
- Part Number: 304-1870 is the designated Caterpillar® dealer part number for this sprocket.
- Compatibility Guarantee: These sprockets are assured to fit the models listed, allowing you to order with complete confidence.
- To extend the life of both sprockets and rubber tracks, it is recommended to change them simultaneously. This practice ensures optimal wear and prevents premature degradation of the undercarriage components.
- In addition to sprockets, our inventory includes a full lineup of undercarriage parts for the 259B3 series compact track loader:
- Front Idler
- Bottom Roller
- Rear Idler
- Triple Flange Idler
- Rubber Tracks, including standard and wide options
재고 219개
Share This Product
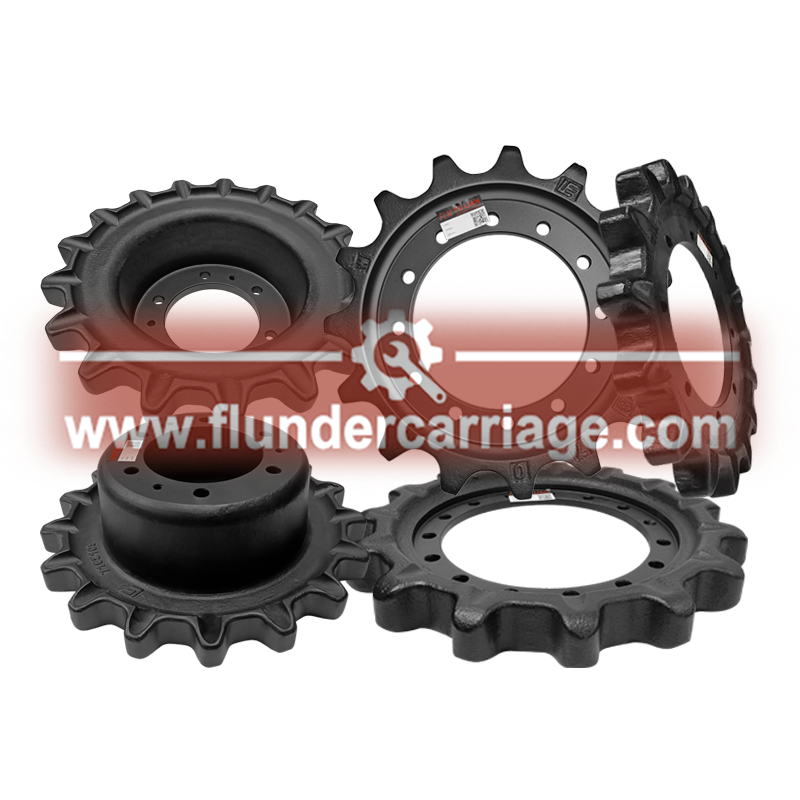
Flundercarriage Show
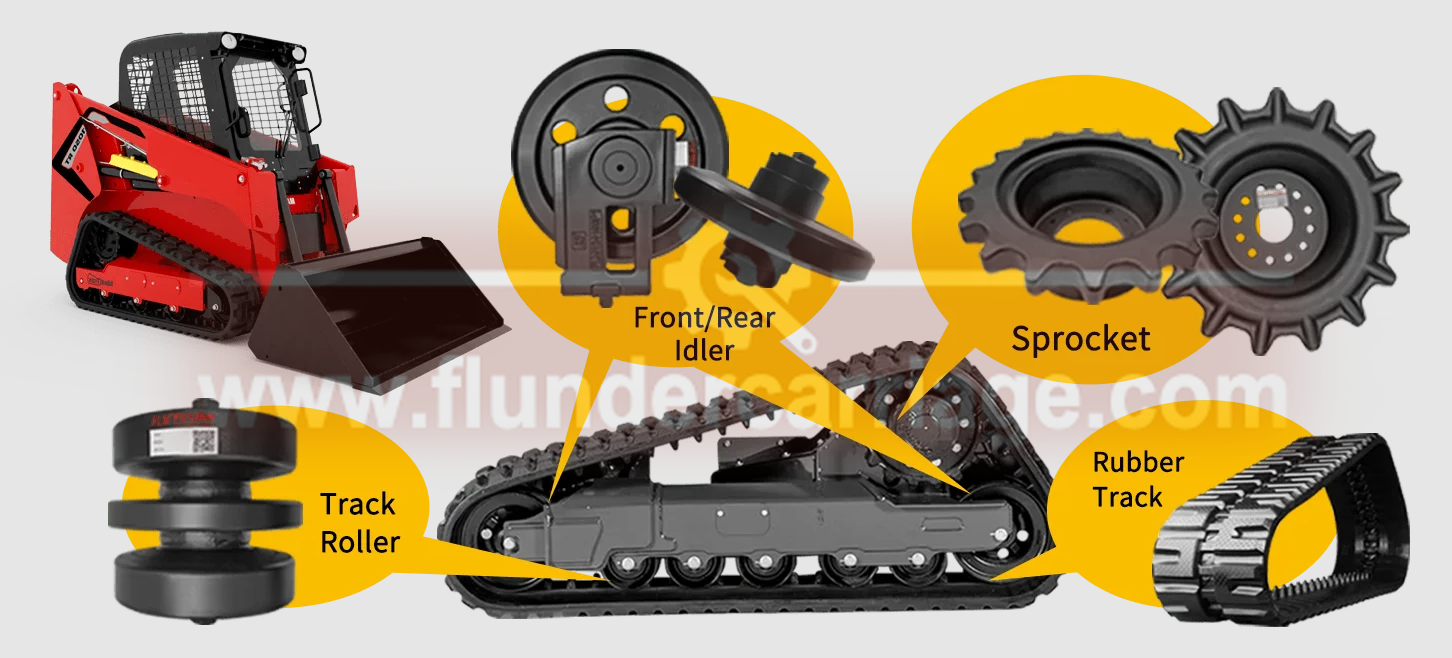
Why Choose FL Undercarriage
-
20+ Years Experience
-
100+ Dealers Globally
-
300000+ stock Keeping units
-
50000000+ USD Annual sales
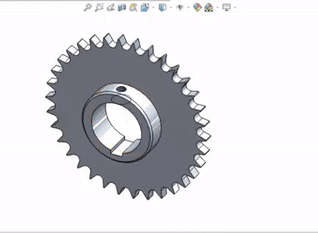
Product Range
Our sprockets are built to withstand extreme conditions, ensuring smooth and efficient power transmission in your machinery. Crafted from high-quality materials, they offer exceptional wear resistance and durability, making them ideal for heavy-duty applications. Trust our sprockets to enhance the performance and longevity of your equipment, keeping operations running smoothly.
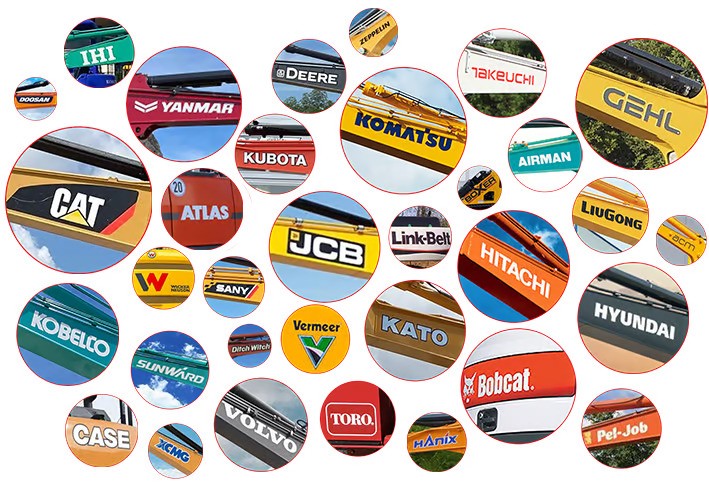
Machinery brands our parts are suitable for Bobcat, Caterpillar, Case, Doosan, GEHL, Hitachi, Hyundai, IHI, Kubota, Kobelco, Komatsu, Pel-Job, Takeuchi, Volvo etc.
How are your sprockets produced
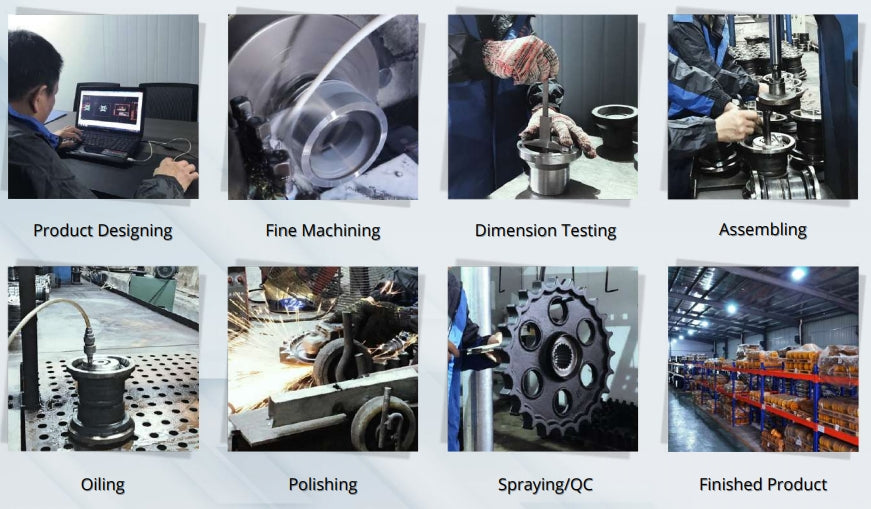
Trade Show Events
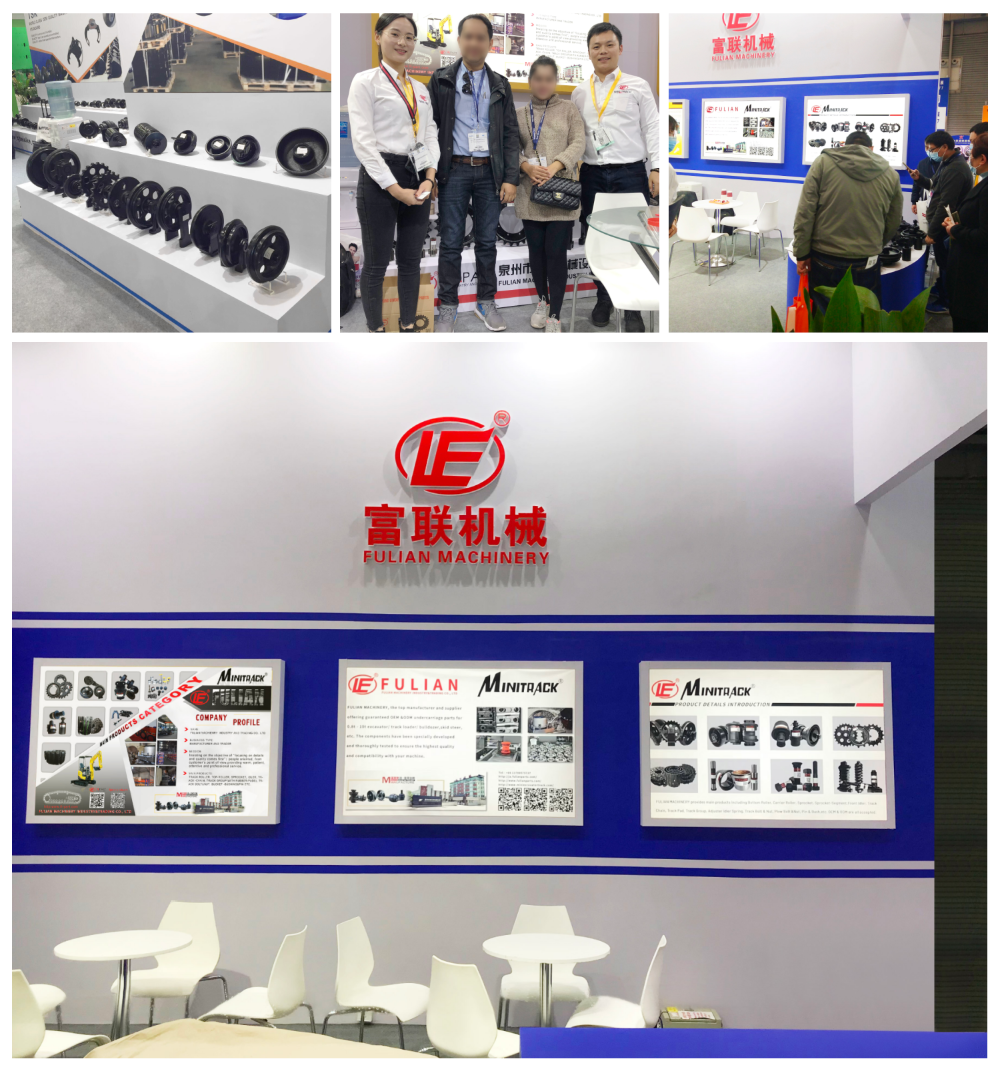
Customer reviews
FAQ
How often do excavator sprockets need to be changed?
A sharp gear indicates that the gear is worn. Check whether there are grooves around and under the gear that are similar to the chain shape. This "shadow" wear indicates that the gear has been seriously worn and should be replaced.
What are the contributing factors that lead to the deterioration of sprockets on an excavator?
Several factors lead to wear and tear of excavator sprockets, including:Heavy usage, Abrasive environments, Improper track tension, Inadequate maintenance, Rough operation, Quality of the sprockets, Misalignment of components, Age and metal fatigue
What maintenance routine can I follow to ensure my excavator sprockets last longer?
To extend the life of your excavator sprockets, implement a maintenance routine that includes:Regular cleaning of debris and dirt,Frequent inspections for wear,Ensuring correct track tension,Prompt replacement of worn parts,Lubrication to reduce friction,Using high-quality replacement sprockets,Operator training to prevent harsh handling.